D.I.Y. Home / Garden
RAPID PROTOTYPING & SMALL BATCH PRODUCTION
Rapid prototyping serves as an invaluable tool for businesses aiming to swiftly iterate and test their product designs, enabling them to refine concepts and identify improvements efficiently. For small batch production runs, 3D printing technologies (FDM) and (SLS) provide a cost-effective and agile solution, enabling companies to produce limited quantities of customized components or products without the need for expensive tooling or lengthy setup times
Fused Deposition Modeling
or FDM 3D Printing
FDM printers work by heating a thermoplastic filament to its melting point and then extruding it, layer by layer, to create a three dimensional object.
FDM printers are relatively inexpensive and easy to use, making them a popular choice for home and small-scale 3D printing

Stereolithography (SLA)
Stereolithography works by using a photopolymer resin that is cured by exposure to light.
The machine traces out the desired geometry layer by layer using a computer-controlled moving laser beam.
The beam is directed by mirrors that are positioned around the build platform.

CAD DESIGN & REVERSE ENGINEERING
When it comes to certain projects, a computer-aided design, or CAD, can be extremely beneficial. A main advantage to using CAD is the fact that it provides experts with greater accuracy. This is done by replacing manual drafting with electronic design software, such as SketchUp, Fusion 360, or AutoCAD Design Edition.
Ever since the inception of our company, we have encouraged every single employee to focus on only one thing- quality. We have always strived to create products that achieve the highest standards and meet our customer's expectations.
No matter the project, we always ensure that each and every element of the project is produced to perfection and is the best possible outcome. We use the best materials and processes to ensure that the quality of our products is unrivalled, and that our customers get the most out of them.
This focus on quality and customer satisfaction has been the cornerstone of our success and has allowed us to build a strong and loyal customer base. Our customers know that when they entrust us with their projects, they will get the best results.
We are proud to have created and maintained so many successful projects over the years and have provided our customers with products that exceed their expectations. We will continue to strive for excellence and never stop searching for new ways to improve our products and services.
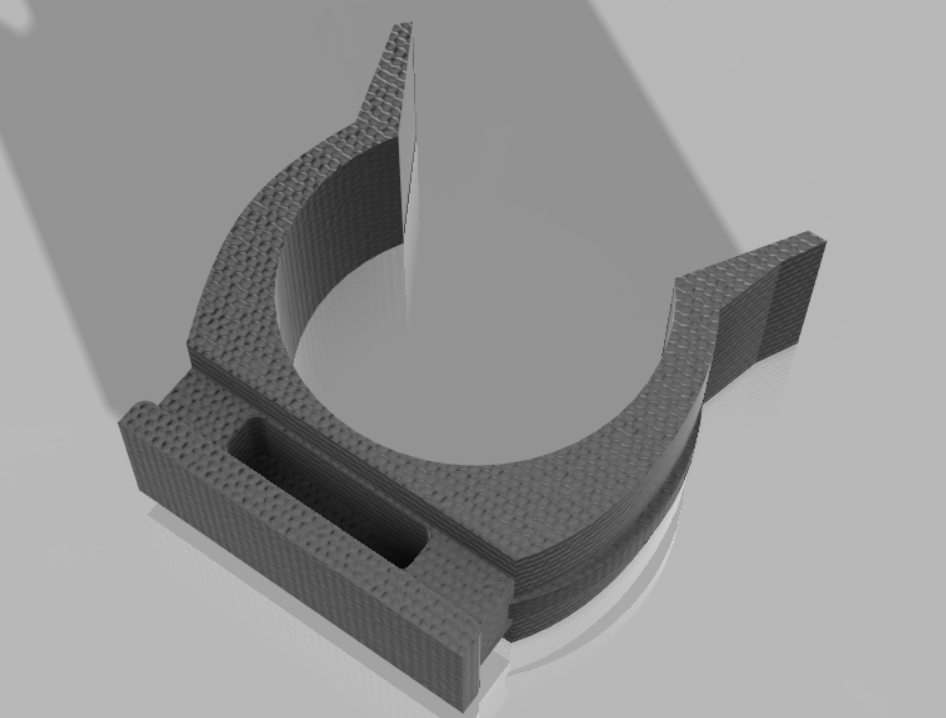
We arrived at the local farm, ready to help out with any projects that needed attention. We had experience in dealing with a wide range of handy work and this time we were met with a broken kickboard in the kitchen. With our extensive knowledge, we knew that we had the capability to reverse engineer and create a small batch of ASA 3D printed plastic clips to fix the plinths.
We got to work, cutting, shaping and fitting the plastic clips together, making sure that they fit perfectly onto the cabinet legs. As we worked, we also discussed ideas on how to make these clips more useful and we thought of other uses they could serve, such as for kitchen plinths, corner posts and filling panels. We then set about testing the clips to make sure that they were durable and stable enough for the job.
Finally, our work was complete and we had successfully created a new and unique set of ASA 3D printed plastic clips. We were pleased with our efforts and the results and we left the farm knowing that our clips would help with the kickboard problem and any other issues that the farm may have.
Our work had been both challenging and rewarding and we walked away satisfied with a job well done. We may never know exactly where our clips will end up, but we take pride in knowing that our hard work has made a difference, no matter where we find them.
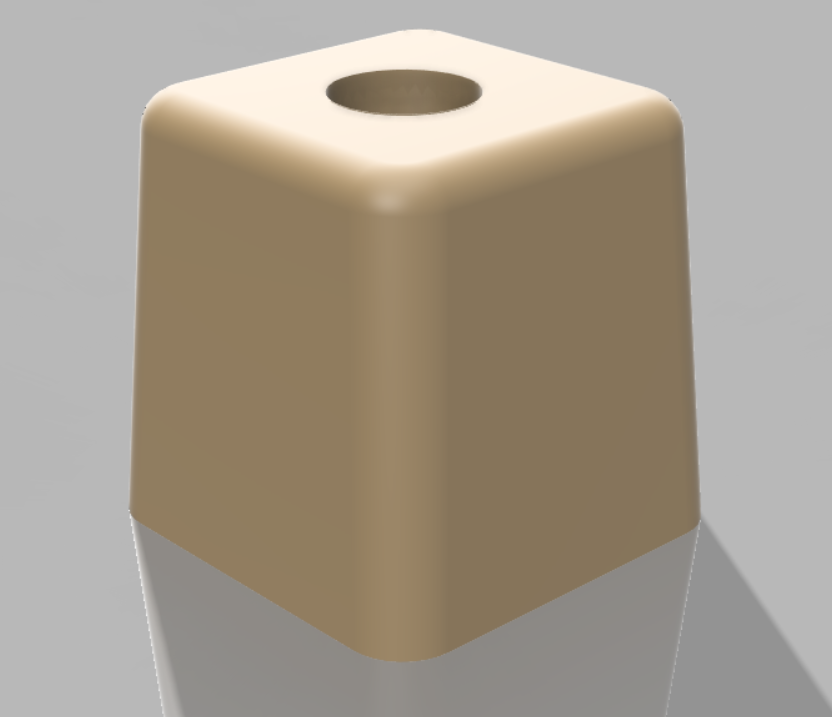
As I worked with the local lady to restore her vintage furniture, I noticed that the legs on her sofa were cracked. We were in a bind—we had looked everywhere for a replacement set but were unable to find them in the market. We needed to find a way to bring this sofa back to life, so we had no choice but to use our own problem-solving skills.
My mind jumped to the possibilities of 3D printing in ABS plastic. By reverse engineering the original legs, we could use our 3D printer and custom-design a set to match. We invested in 100% infill to ensure we had the necessary strength and durability in the 3D printed parts.
With a few tweaks and adjustments, we had a brand-new set of legs on the sofa. The pieces fit perfectly and we still couldn't believe the result! It was like the couch had never had a broken leg to begin with.
The sofa was a beautiful reminder of the power of innovation. From the earliest examples of sofas being mere futons or cushions laid on the floor, to couches with raised legs, technology has allowed us to bring back furniture in a way we never thought possible.
The local lady was ecstatic with her restored piece and I was proud to have been a part of the process. The experience left me feeling excited and energized, and I couldn't help but wonder what other projects were out there waiting to be solved.
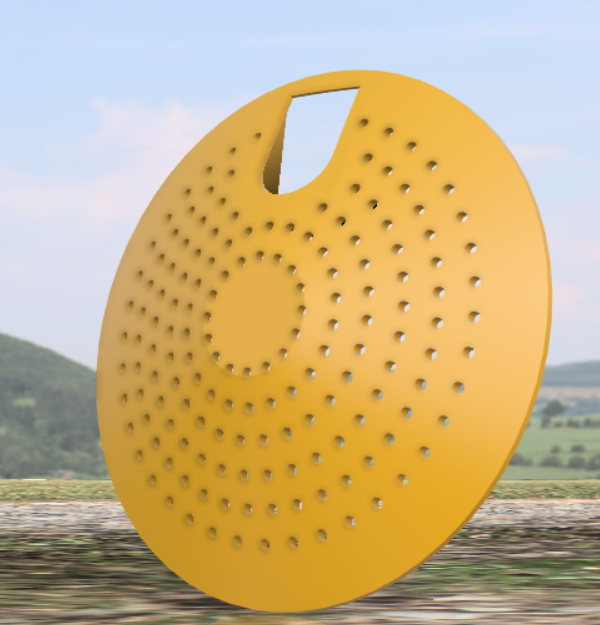
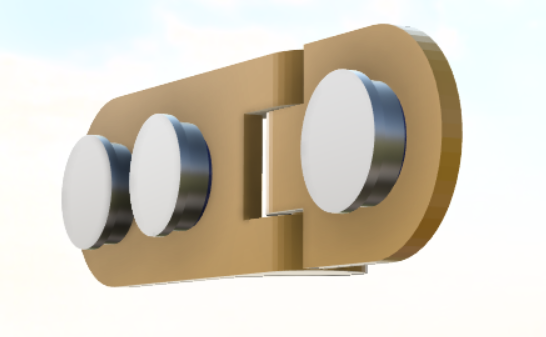
