Multi Jet Fusion (MJF)
There are two main types of 3D printing technology: material jetting and material extrusion. Each has its own advantages and disadvantages, but the main difference between the two is the heat source.
SLS uses a laser to scan and sinter each cross section, while in MJF an ink (fusing agent) is dispensed on the powder that promotes the absorption of infrared light. An infrared energy source then passes over the building platform and fuses the inked areas.
MJF is generally considered to be more precise than SLS, and is better suited for complex geometries. It is also slower, and the build platform must be heated to a high temperature (around 200 degrees Celsius) in order to properly fuse the powder.
SLS, on the other hand, is faster and can be used with a wider variety of materials. The build platform does not need to be heated, as the laser itself is used to raise the temperature of the powder. However, SLS is less precise than MJF, and the finish quality is not as good.
MJF is the superior technology for most applications, but SLS has its advantages as well. It really depends on what you need the 3D printed object for as to which technology is best suited.
3D printing technology has come a long way in recent years. Multi Jet Fusion (MJF) 3D printing is now being used in a variety of applications, from manufacturing and medicine to architecture and custom art and design.
MJF 3D printing is particularly well-suited for manufacturing applications. It can produce parts with very tight tolerances, and the parts can be made from a variety of materials, including metals, plastics, ceramics, and glass.
MJF 3D printing is also being used in medicine, for both prosthetic devices and implants. The ability to print complex shapes in medical-grade materials means that MJF 3D printing can create customised devices that are perfect for each patient.
Architecture is another area where MJF 3D printing is having an impact. The ability to create complex, free-form shapes means that MJF 3D-printed buildings can have a truly unique appearance. And, because MJF 3D-printed parts can be made from a variety of materials, they can be used to create buildings that are both beautiful and functional.
The applications of MJF 3D printing technology are limited only by the imagination. As the technology continues to develop, it will no doubt find even more uses in the years to come.
Multi Jet Fusion uses a powder bed and an array of inkjet nozzles to deposit droplets of a fusing agent onto the powder bed. The fusing agent binds the powder together to create a solid layer.
This process is then repeated, layer by layer, until the part is complete.
The advantage of Multi Jet Fusion over other 3D printing processes is its speed. It is capable of producing parts at a rate of up to 8 kg per hour, which is orders of magnitude faster than the traditional processes.
In addition, the process is more accurate and produces parts with a higher degree of dimensional accuracy and consistency.
The Multi Jet Fusion process is also more versatile than other 3D printing processes, as it can be used to produce parts with a wide range of material properties.
The process is not without its challenges, however. One of the challenges is the need for a high degree of control over the process parameters to produce parts with the desired material properties.
Another challenge is the need for a robust powder management system to prevent the powder from becoming contaminated with the fusing agent.
Despite these challenges, Multi Jet Fusion is a game-changing technology that is poised to revolutionize the world of additive manufacturing.
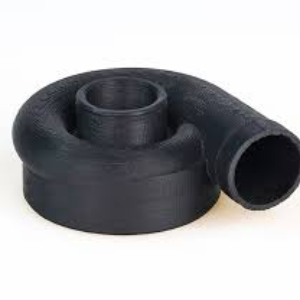