Fused Deposition Modeling (FDM)
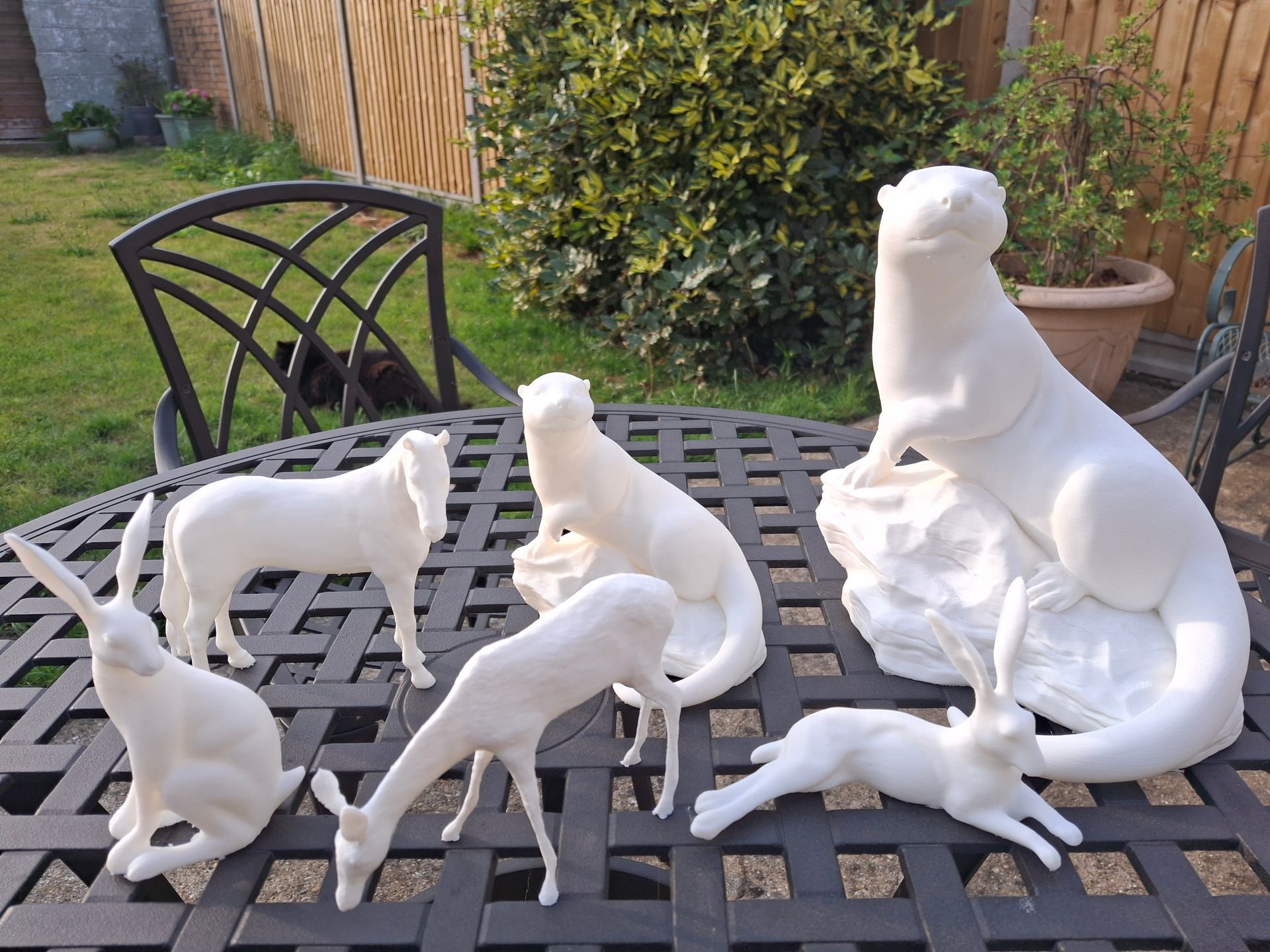
Fused Deposition Modeling, or FDM, is the most widely used type of 3D printing. FDM printers work by heating a thermoplastic filament to its melting point and then extruding it, layer by layer, to create a three dimensional object.
FDM printers are relatively inexpensive and easy to use, making them a popular choice for home and small-scale 3D printing. However, FDM printing is not without its limitations. The main drawback of FDM printing is that it is relatively slow compared to other 3D printing technologies.
Another limitation of FDM printing is the range of materials that can be used. Thermoplastics are the only type of material that can be used with FDM printers. This limits the range of objects that can be printed with FDM technology.
Despite its limitations, FDM printing remains the most popular type of 3D printing due to its affordability and ease of use.
Fused Dispositioning Moulding, also known as FDM, is a 3D printing process that is becoming increasingly popular for both home and industrial use. FDM works by melting a filament of plastic and extruding it through a small nozzle. The plastic is then layered on top of itself to create a 3D object.
There are many advantages to using FDM over other 3D printing processes. One advantage is that FDM is much cheaper than other processes. This is because FDM printers are relatively simple to build and the plastic filament is relatively inexpensive.
Another advantage of FDM is that it is very versatile. FDM printers can print in a wide variety of materials, including PLA, ABS, PETG, and even metal. This makes FDM an ideal choice for printing objects that need to be strong or heat-resistant.
Finally, FDM is relatively easy to use. Most FDM printers come with easy-to-use software that makes it simple to create 3D models. Once the model is created, the printer does the rest of the work.
Overall, FDM is a great choice for 3D printing. It is relatively inexpensive, versatile, and easy to use. If you are looking for a 3D printing process for your home or business, FDM is a great option to consider.
FDM 3D printing is a technology that works both horizontally and vertically, where an extrusion nozzle moves over a build platform. The process involves the use of thermoplastic material that reaches melting point and is then forced out, to create a 3D object layer by layer. In the early days of automobile production, engineers and designers would often create prototypes by hand. This was a time-consuming and expensive process, and it was difficult to create complex shapes. Then, in the 1980s, a new technology called fused deposition modeling (FDM) was developed.
With FDM, a prototype can be created quickly and cheaply. And, since it is an additive manufacturing technique, it can be used to create complex shapes that would be difficult to produce by other means.
Today, automotive 3D printing is used by many different industries, ranging from aerospace to consumer products. It is particularly well-suited for creating prototypes and small batch production runs.
Automotive 3D printing has transformed the automobile industry, allowing manufacturers to test new designs quickly and cheaply. It has also allowed the production of lightweight tools and final functional components.
Thanks to automotive 3D printing, the automobile industry is able to innovate at a faster pace than ever before.
Fused Deposition Modeling, otherwise known as FDM, is the most widely used type of 3D printing. It works by extruding thin layers of melted plastic, one on top of the other, to build up a three-dimensional object. This process is relatively fast and inexpensive, making it a popular choice for consumers and businesses alike.
If you're interested in using FDM to create your own products, there are a few things you should know. First, you'll need to find a company that offers instant online quotes. This will help you get an idea of how much it will cost to print your desired object. Second, you'll need to choose the right type of plastic for your project. ABS plastic is a common choice for FDM printing, but there are other options available as well. Lastly, you'll need to have a design ready to go. This can be created with a CAD program or by using a 3D scanner.
Once you have all of these things squared away, you're ready to start printing! FDM is a great way to create prototypes, one-of-a-kind objects, and even functional parts for use in everyday life. With a little bit of planning and preparation, you can use this versatile technology to bring your vision to life.
