Kingsley Cars Project
RAPID PROTOTYPING & SMALL BATCH PRODUCTION
Rapid prototyping serves as an invaluable tool for businesses aiming to swiftly iterate and test their product designs, enabling them to refine concepts and identify improvements efficiently. For small batch production runs, 3D printing technologies (FDM) and (SLS) provide a cost-effective and agile solution, enabling companies to produce limited quantities of customized components or products without the need for expensive tooling or lengthy setup times
Fused Deposition Modeling
or FDM 3D Printing
FDM printers work by heating a thermoplastic filament to its melting point and then extruding it, layer by layer, to create a three dimensional object.
FDM printers are relatively inexpensive and easy to use, making them a popular choice for home and small-scale 3D printing

Stereolithography (SLA)
Stereolithography works by using a photopolymer resin that is cured by exposure to light.
The machine traces out the desired geometry layer by layer using a computer-controlled moving laser beam.
The beam is directed by mirrors that are positioned around the build platform.

CAD DESIGN & REVERSE ENGINEERING
When it comes to certain projects, a computer-aided design, or CAD, can be extremely beneficial. A main advantage to using CAD is the fact that it provides experts with greater accuracy. This is done by replacing manual drafting with electronic design software, such as SketchUp, Fusion 360, or AutoCAD Design Edition.
I had always been fascinated by the older cars. Something about the artistry of their construction, the way they were put together by hand, the way they called to me to take them apart and put them back together. It was a passion of mine, and I was lucky enough to find an opportunity to combine my love of cars with my career.
That opportunity took the form of a project to restore an old car. We were asked to work on a project that meant a lot to me because of my affinity for these vintage beauties. We had a team of experts with a variety of skills, but it was clear that I had the most knowledge and experience when it came to the fine details of the car restoration and retrofitting.
We worked tirelessly, and it was incredibly rewarding. We had a deep shared understanding of the car and the process, and I felt that I was able to bring my expertise to the table in a way that was meaningful and beneficial. As we made progress, I felt my love for the car only grow.
As I watched the car roar off into the distance, I couldn't help but feel a little bit nostalgic. It felt like a special moment that would stay with me forever. I knew that this project meant a lot to me, and I was grateful to have had the opportunity to work on it.
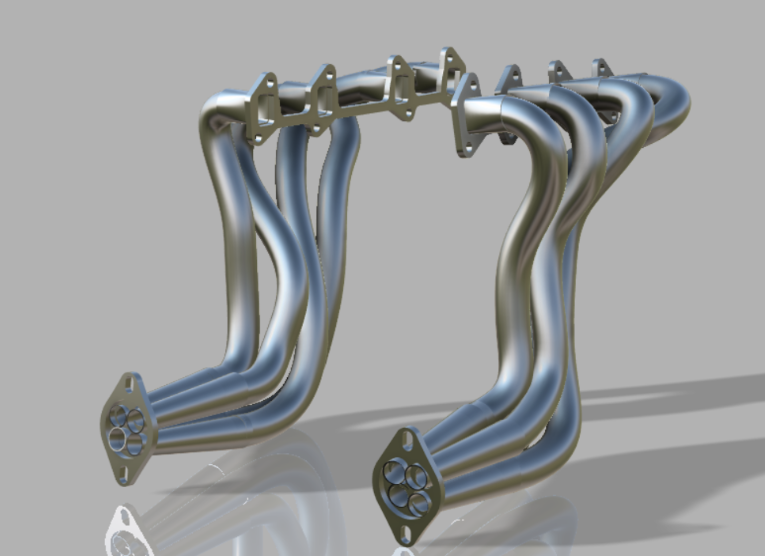
It began as a fairly simple project, but then, as if it was destined to be different, something happened. During the detailed scan, it was noticed that the inlet and exhaust manifold were impossible to replicate perfectly. The technicians had been scanning and replicating components perfectly until this point, but this one component seemed to be a challenge.
It made them curious and they decided to further investigate the matter. The team could not believe their eyes when they discovered that the exhaust manifold was no ordinary component. It seemed to have a special property that made it incredibly hard to replicate.
We dug deeper and eventually uncovered that the exhaust manifold had a special coating that made it heat-resistant and also gave it the ability to keep the exhaust gases from making their way out. This meant that the gases were held responsible for the power of the engine.
The engineers were amazed and speechless. They had never seen anything like it before. It seemed to be something right out of a science fiction novel. After all the research, they had to admit that this component was unique.
The team realized that replicating this component was a difficult but a necessary task. It was the only way they could make sure their project was successful. They worked diligently to make sure they got it right, and in the end, they did.
The final product was extraordinary and powerful. The team was proud of their work and the knowledge they had gained through their discovery. It was a breakthrough moment and it showed that dedication and hard work really do pay off.
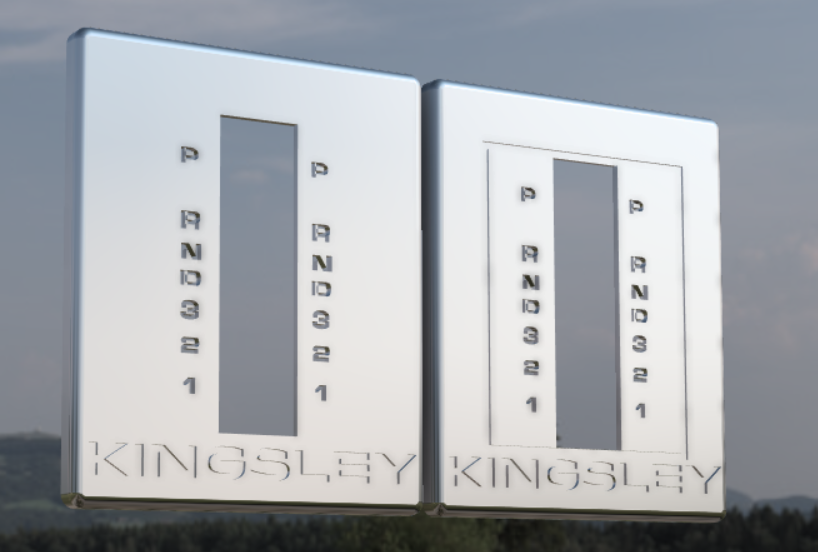
The team had been tasked with a daunting challenge: replicate and modify two gear shift covers, one to be covered with leather and the other to be left plain. The team had grown accustomed to these kinds of tasks, and they drove themselves to meet the deadline set by the company.
Our expertise was put to work as we took the lead on the project, reverse engineering the item and creating two 3D models that would be used by the rest of the team to modify the gear shift covers. Working diligently and efficiently, the team was soon able to incorporate the logo into the design, adding the final touches that made the covers truly unique.
With their work complete, the engineering team proudly packed up their materials and sent the finished products back to their employer. But as they were leaving, a curious thought occurred to me: how would the gear shift covers actually work?
Determined to find out, he grabbed the materials and returned to the shop, where he quickly set up a test drive in a nearby parking lot. After engaging the transmission into neutral and pressing the low button to change the range, the message center informed John that the maximum speed for the range change had been reached - a testament to the team's precision and dedication.
I then engaged the drive and gave the vehicle a test run, and soon enough, I was convinced that the engineering team had done an impeccable job. As I returned to the shop, could only think of one thing: the pride in knowing that our team had achieved something remarkable.

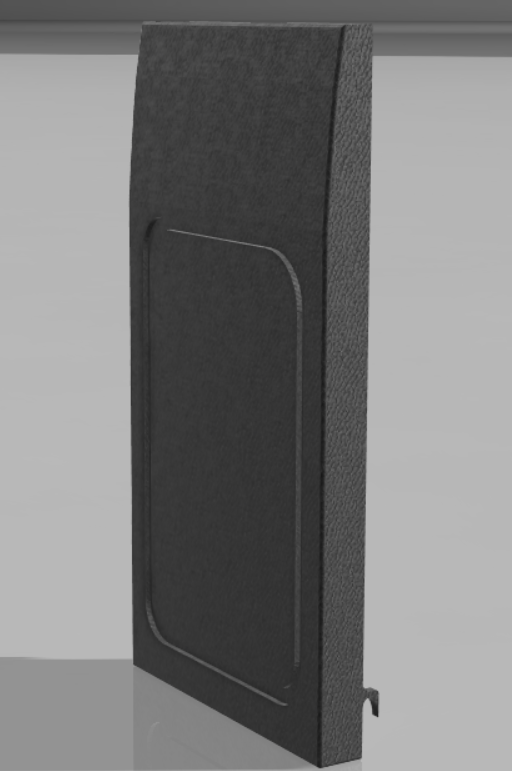