Can you 3D Print Ceramics?
Yes, You Can 3D Print in Ceramic! 3D Printing Tips from the Experts

With the ever-expanding universe of 3D printing materials, it’s hard to know where to begin. Which material is best for my project? How do I pick a 3D printer that will enable me to print in that material?
If you’re struggling to find your way through the maze of available materials, we’ve got you covered. In this blog post, we cover three different ceramic 3D printing tips and techniques.
Each one is useful in its own right. But more importantly, together they give you all the tools you need to kickstart your career as a ceramics specialist in the world of additive manufacturing.
What is Ceramic 3D Printing?
Ceramic 3D printing is a subset of the larger category of ceramic additive manufacturing. Ceramic materials, unlike metals or plastics, are not “endothermic.” That is, their chemical reactions don’t generate their own heat, so the ceramic additive manufacturing process is carried out at an elevated temperature (2350°C).
Ceramic additive manufacturing is a process that gradually deposits ceramic powders on a build platform to create a ceramic part layer by layer.
The high temperatures of the process cause the powders to melt together, fusing together to create a strong, solid ceramic object.
Which Materials Can Be Used for Ceramics Printing?
While the ceramic additive manufacturing process allows the creation of ceramic parts in a wide variety of ceramic materials, ceramic 3D printing is primarily focused on three:
- Rigid-Darkened: A mixture of ceramic powders and metal oxides (e.g., iron, cobalt).
- Slip Casting: A ceramic-rich clay that is suitable for creating complex shapes.
- Varied Shapes: A fine-grained ceramic powder that contains no clay additives.
How to Select a Ceramic Material for 3D Printing?
Let’s be honest — you won’t know which ceramic material is best for your application until you’ve printed with a few different ceramic 3D printing materials. However, for a basic guide, keep the following points in mind:
- Start with the simplest ceramic material.
- Choose a ceramic that has excellent thermal properties.
- Use a ceramic with a high Young’s modulus.
- Pick a ceramic with a high shear strength.
- Evaluate the cost of each ceramic material.
- And consider what color ceramic additive material you would like to print in.

Tips for Successful Ceramic 3D Printing
While there are many ways to get the most out of ceramic 3D printing, there are also a few pitfalls to avoid. Here are our top tips for successful ceramic 3D printing:
- Use a ceramic-friendly build platform. Tiles and ceramic boards are a great option.
- Make sure you’re using a ceramic-friendly nozzle. Ceramic nozzles are specially designed to handle high-temperature materials.
- Make sure you’re using a ceramic-friendly support material. Ceramic supports will be more brittle than metals and plastics.
- Ceramics are best printed with a low nozzle temperature (1250°C vs. the typical 1450°C).
However, to avoid thermal shock, be sure to let your ceramic part cool down before removing it from the build platform.
Define Your Material Requirements
First, decide if you want to print with a rigid or a non-rigid ceramic material. A rigid ceramic material will have a high thermal conductivity, a high thermal capacity, a low coefficient of thermal expansion, and a high shear strength.
A non-rigid ceramic material will have a low coefficient of thermal expansion, a low thermal conductivity, and a high shear strength. From there, consider the weight of your ceramic part. A heavier ceramic will travel slower through the extruder, creating a wider part with less detail.
A lighter ceramic will travel faster through the extruder, enabling you to create more complex shapes in a single print. Along the same lines, consider the diameter of your ceramic part.
A smaller ceramic will create finer details, while a larger ceramic will allow you to create more complex shapes in a single print.
Print with Rigid-Darkened Ceramic
If you want your ceramic part to be hot-fired, start with rigid-darkened ceramic. Rigid-darkened ceramic material is a mixture of ceramic powders and metal oxides that are designed for high strength and thermal stability.
This ceramic additive material will allow you to create complex geometries that are suitable for both functional and aesthetic applications. To create a rigid-darkened ceramic part, start by preparing your ceramic build. Be sure your build platform is the right size and shape, and the build is free of any defects. Next, select a ceramic-friendly material for your build.
We recommend a high-strength ceramic-based epoxy. Once your build is prepared, create your ceramic part design in CAD. Because ceramic parts require a larger build volume, we recommend that you at least double the minimum print volume of a comparable plastic or metal part.
Finally, use a ceramic-friendly CAD software to generate your build instructions. For example, Autodesk MeshMixer can be used to create a ceramic build.
Add Color with Slip Casting
For a ceramic part that is designed to be decorative, start with slip casting. Slip casting is a ceramic-rich clay that is designed for low thermal expansion and a low coefficient of thermal expansion. This ceramic additive material can be easily colored, making it ideal for decorative applications
— like adding a colorful touch to an architectural design. To create a decorative ceramic part, start by preparing your ceramic build. Be sure your build platform is the right size and shape, and the build is free of any defects. To design your ceramic part, start with a decorative two-dimensional sketch.
From there, use a ceramic-friendly CAD software to generate your build instructions.
For example, Autodesk MeshMixer can be used to create a decorative ceramic build.
Add Strength with Varied Shapes
If you want your ceramic part to be highly functional, start with a ceramic additive material that is low in thermal expansion and has a low coefficient of thermal expansion. To create a functional ceramic part, start by preparing your ceramic build.
Be sure your build platform is the right size and shape, and the build is free of any defects. Next, select a ceramic-friendly material for your build. We recommend a high-strength ceramic-based epoxy. Once your build is prepared, create your ceramic part design in CAD.
Because ceramic parts require a larger build volume, we recommend that you at least double the minimum print volume of a comparable plastic or metal part.
Once your design is done, use a ceramic-friendly CAD software to generate your build instructions.
For example, Autodesk MeshMixer can be used to create a functional ceramic build.
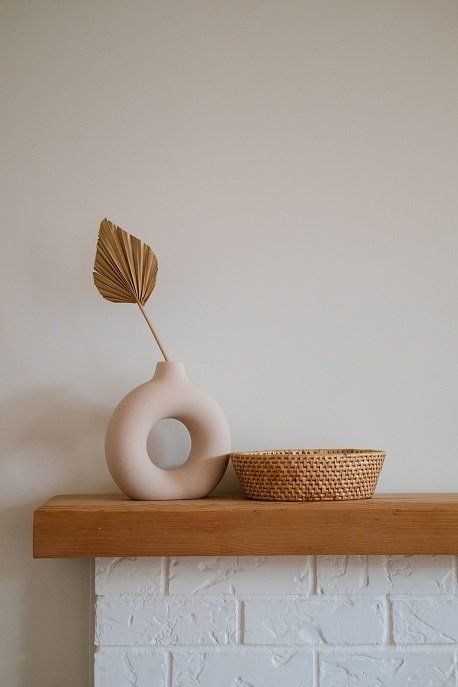
Conclusion
Ceramic 3D printing is a powerful technology that allows you to create unique, high-quality ceramic parts. Start by deciding whether you want to print with a rigid or non-rigid ceramic material. From there, choose a ceramic additive material that has excellent thermal properties.
Finally, be sure to use a ceramic-friendly build platform, a ceramic-friendly nozzle, and a ceramic-friendly support material to ensure that your ceramic part comes out defect-free.
And, most importantly, have fun! Ceramic 3D printing is a fascinating technology that can be used in a wide variety of applications.
With these ceramic 3D printing tips and techniques, you can create ceramic parts that are beautifully colored, rich in detail, and as strong as iron.