Understanding the Process of 5-Axis Machining
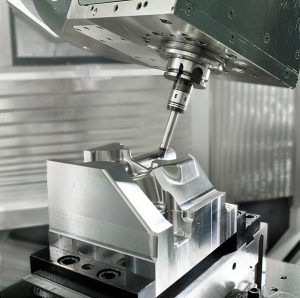
Many of you might have had some experience with 5-axis machining, but for those new to the technology, let’s break it down.
A machine that is capable of 5-axis design can move the toolpath in the X, Y, and Z directions as well as rotate in the A and B (or C) axes – thus the term 5-axis machining. Having those two extra axes compared to traditional 3-axis machining allows for greater flexibility in part design and more fluid movements for the mill head. It also means that you as the operator don’t have to do as much setup time for milling different sides of a certain part.
In terms of popularity, 5-axis CNC machines are highly preferred for aerospace applications. With that said, 5-axis machines can be used in any application where a 3-axis machine is already implemented. The advantage then becomes cycle time and tool changes, among other things. Think of the process of milling a shape out of a block of aluminum. In a 3-axis setup, the operator would have to change the orientation of the part at least once as well as possibly change tools. With the more automated or sometimes called “done in one” 5-axis CNCs, you can set up a part to be milled and the machine will handle all of the movements for virtually all of the faces of the part. It’s a similar comparison to a printer that requires you to re-feed the paper when you want to print double sided versus a printer that does this process automatically.
If you are still having trouble visualizing how exactly a 5-axis machine functions, refer to the diagram to the right. You can see the traditional cartesian X, Y, and Z axes and 3 rotational axes labeled A, B, and C. In a 5-axis machine, the tool head is capable of moving in the X, Y, and Z planes as well as the A and B rotational axes. 6-axis machines are of course a possibility, and they do exist. However, 6-axis functionality presents little advantage over 5-axis machining, so 5-axis is mainly used.
So, are there advantages then for a machine to have the capabilities to rotate along the A and C axes rather than the A and B axes? Well, yes – and each machine can be set up in various configurations. For example, a trunnion-style style 5-axis machine uses the A and C axes and a swivel-rotate style machine rotates about the B and C axes. In a trunnion machine, the table in the machine is what facilitates the rotation. In a swivel-rotate machine, the spindle handles the rotation. Digging even further into machine orientation, there are even machines that have multiple spindles allowing for even more precise and complex part production. All of this variation ultimately hinges on the many applications a machine will be used for.
To get more into certain niches and machining areas where 5-axis machines present advantages, let’s first look into mold making applications. Think about making a plastic injection mold for a part that requires deep precise cuts. Using a 3-axis machine, you would need to slow down the feed rates and use long tools to cut the mold precisely. Getting the proper surface finish in the mold with a 3-axis machine can even still prove to be difficult. These are all problems that are solved with 5-axis milling operations. Within virtually all applications of milling, 5-axis machines can overcome the hiccups commonly found when using 3-axis machines.
There are virtually endless complexities when it comes to using machines of all types, but this should serve as a brief explanatory introduction to the processes of 3-axis versus 5-axis machining.
Sources:
5-axis
,
engineering.com
,
Mazak
Images:
[1]
,
[2]
The post Understanding the Process of 5-Axis Machining appeared first on Inventor Official Blog.